热轧带钢卷形控制分析
摘要:热轧带钢卷形问题是影响带钢质量的重要因素。本论文针对热轧带钢卷取过程中产生的卷形问题,从控制模型及工艺操作、设备管理因素等方面对各类卷形进行分析和研究,解决卷取卷形不良问题,提高成材率和经济效益。
1 前言
卷形作为卷取区域重要和难控制的事项,如发生问题会影响后道工序能否正常的运行, 严重时会造成主轧线短时间的非计划停机。卷形塔形在可处理范围内时,可通过平整线、重卷线、 横纵切线等精整线处理,但随之增加额外成本,但 是,塔型在运输过程中重心偏,造成运输链、步进梁掉卷,砸坏设备,严重时影响正常生产。
2 卷形缺陷及产生原因
卷形不良的主要缺陷是塔形。塔形根据类型 分为内塔( 头塔) 、外塔( 尾塔) 、中间塔( 层间错动、锯齿) 三种。如图 1 所示典型的卷形不良。
1)内塔:头部内圈偏向一侧严重,形成塔形。因来料跑偏严重或带钢头部镰刀弯,侧导板夹持 纠偏,将中心线重新调回,产生塔形。助卷辊单侧磨损严重或水平度不好,也会加剧塔形的产生。
2)外塔:尾部十几圈范围内,带钢偏向一侧, 形成钢卷尾部塔形。带钢尾部出精轧末机架后, 夹送辊两侧压力偏差变大,侧导板夹持不住带钢, 造成中心线跑偏形成塔形。
3)中间塔:钢卷中间部分带钢两侧交叉错动, 两侧不平整,形似锯齿。因精轧末机架与卷取夹 送辊之间张力波动大、速度不匹配造成失张严重 使得带钢运行不稳定,侧导板夹持力不足,带钢在侧导板之间游荡、上下抖动。根据塔形产生原因可分为设备原因、工艺原因和操作原因。
2.1 设备原因
1)侧导板对中度偏差大、磨损严重,造成夹持 不住带钢产生塔形;
2)夹送辊水平度不好、磨损严重,上下辊之间两侧辊缝不一致,易在卷取时产生塔形;
3)助卷辊、卷筒水平度偏差大、磨损严重,造成两者之间辊缝偏差大,导致带钢头部不能平行通过助卷辊而产生塔形;
4)卸卷小车托辊水平不好,定尾时产生塔形; 定尾完成后托辊锁不住、钢卷在小车上打滑都易造成塔形; 卸卷小车时序控制异常,也会造成 塔形;
5)检测原件失真或异常。生产时头部到达夹 送辊,系统未检测到受载信号而没有发出信号,或接收到受载信号,但分析处理时间过长,造成建张时序( 助卷辊打开、卷筒涨径) 错误和侧导板第二 次短行程动作时序异常;
6)设备运行不稳定:位置精度不好、液压稀油系统故障、标定不准等;
7)电气运行不稳定:传动连锁保护不全、传动不稳定、控制元件故障、数据传输异常( 转矩、张 力、位置、压力、速度、卷取温度、跟踪等) 、控制逻辑异常等。
2.2 工艺原因
1)精轧来料问题: 跑偏严重、镰刀弯、S 弯、凸 度异常、楔形大、浪形、卷取温度低等问题都会产生塔形;
2)侧导板控制时序,两侧动作不一致会将带 钢头部撞向侧导板动作偏慢的一侧,产生塔形;
3)侧导板开口度设定不当,薄规格速度快,侧导板动作速度恒定,开口度设定偏大,动作时间就偏长容易产生塔形。
2.3 操作原因
1)数据给定不合适,例如超前率、滞后率、张力等都会产生塔形;
2)设备点检不及时、设备更换不及时;
3)技能差,未按规定操作、误动作、监控不及时、调整不及时等。
3 改进方法
设备和操作原因暂且不谈,本节重点阐述工艺方法改进措施。
3.1 侧导板开口度的设定及控制
侧导板位于卷取机夹送辊前方,主要用于引导带钢进入夹送辊并对带钢进行对中和夹持,保证卷形的稳定。侧导板控制分为压力控制和位置控制两种控制模式。
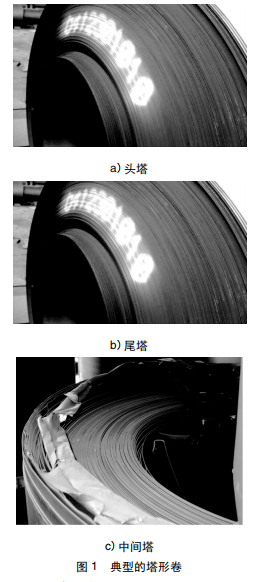
3.1.1 开口度设定
主要分为以下五个阶段:待机:XSG = B + S1 式中:XSG:侧导板的计算机设定值,mm;B:带钢的目标宽度,mm; S1:一次短行程量,一般 S1 = 100mm。
1)在导板入口处检测到钢带头部后,两侧对 称关闭至距导板两侧 30mm 处。XSG = B + S2( S2 = 30mm) ;
2)带钢头部到夹送辊处后,检测到信号激活 二次短行程,通过短行程液压缸开始运动,关闭导板固定钢带直至建立后张力;
3)建立后张力后,为防止伸缩,操作侧导板位置应固定,传动侧导板移动到已测定的宽度位置。压力控制通过传动侧侧导板调整位置实现;
4)当带钢尾部进入夹送辊后恢复到待机设定值。
3.1.2 侧导板的控制时序
为了避免位置跳跃,所有的设定值都是按一 定的斜率慢慢靠近的。手动干预和设定的斜率存储在内部参数中,也可以变化。这些设定值被液压缸的大和小位置所限制。如果没有预先选择操作模式,侧导板的当前位置视为设定值。在自动位置模式下,入口侧导板操作侧参考 开口度为实际带钢宽度加上操作侧和传动侧的短行程。如果没有带钢在侧导板之间,这个短行程作为一个附加值被应用。
一旦带钢头部进入夹送辊,操作侧关闭到带钢宽度的一半,然后保持位置控制。这个传动侧位置设定值将变成带钢宽度的一半减去一个可调整的值(10mm) 。如果传动侧碰到带钢的边部,实际压力增加到一个值,当这个值高于设定压力值, 侧导板会将压力自动控制到计算的压力。在压力控制时序的过程,设定压力值会根据操作侧和传动侧实际压力的偏差进行适应。如果带钢与传动侧建立一个横向力,操作侧检测到的真实压力有所减少,相对于传动侧的设定压力偏差将增加。在压力控制下,传动侧侧导板的导向过程中,真实位置和设定位置的偏差是可控的。如果这个偏差超过计算值( 导板使带钢褶皱) ,压力控制不可用, 侧导板将进行位置控制,并打开到带钢宽带的一半。
当带钢尾部离开侧导板前的热检并加上时间延迟,侧导板将打开一个设定的短行程。当带钢尾部进入夹送辊前的热检检测区域,侧导板将会为下一块钢做准备。
3.2 夹送辊控制
操作工可根据夹送辊两侧压力偏差,对抛尾后两侧压力进行调整,防止两侧压力偏差大引起带钢跑偏,提前调整两侧压力进而改善卷形。
3.3 卷取张力设定
卷取张力对卷形的影响很大。张力设定:T = w × h × t 式中:T-总张力,N;w - 成品宽度,mm;h-成品厚度,mm;t-单位张力,N/mm2,单位张力根据二级系统中查表法计算得出,带钢厚度不同,单位张力也不一样。 张力设定过大,会造成带钢局部拉伸变窄,超标会造成后道工序重卷将窄尺部分切除,影响成材率并增加成本。张力设定偏小,会造成卷取不紧,卷形不良形成面包卷、扁卷。程序设定为未卷钢前有个较小的初始张力,建张后为恒张力卷取。在带钢尾部到 F3 时,抛尾减张力控制投用(-20% ~-40% ),避免末机架抛钢张力变化大造成带钢尾部运行不稳定。带钢尾部以一个较小的张力稳定运行,直至卷取完毕。
3.4 超前率、滞后率设定
根据现场头尾部卷形,调整超前率和滞后率。头部卷不紧需要加大超前率,尾部松、卷不紧需要加大滞后率。数据给定:
1)热输出辊道给定 10% ~ 25% ,按照辊道分段控制速度逐段递增。滞后率一般给定在 10% ~ 20% 。带钢越薄,滞后率越大,减速点越靠近卷取机; 带钢越厚,滞后率越小,减速点越靠近精轧末机架;
2)夹送辊超前率为 5% ~ 15%,滞后率为 5% ~ 10% ;
3) 助卷辊超前率为 10% ~ 35% ;
4) 卷筒超前率为 8% ~ 20% 。
4 设备保养、电气优化、规范操作
通过原因和措施改进分析,从设备定期保养、电气优化和规划操作入手,确保卷型控制。
4.1 设备保养
定期进行设备保养维护,保证设备精度。 1) 侧导板位置偏差 ± 2mm,磨损量 5mm 以 内,对中度偏差 ± 2mm,侧导板与辊道间隙小 于 3mm; 2)夹送辊两侧位置偏差 1mm,辊缝定位精度 ± 0.1mm,水平偏差 ± 0.2mm,压力偏差 ± 10kN; 3) 助 卷 辊 定 尾 精 度 ± 0.1mm,压 力 偏 差 ± 5kN;4) 卷筒: 收缩位727mm,初涨位745mm, 终涨位770mm。
4.2 电气优化
1) 侧导板在夹送辊触发信号异常不动作时,可在程序设定一次短行程动作几秒后启动,避免第二次短行程不动作产生塔形;
2) 对张力修正程序进行优化,在操作台面进行加减张力,每次调整量控制在单位张力的 5% ;
3) 助卷辊压尾优化,在尾部到达侧导板时,选 定的压尾助卷辊进行压靠,压靠压力可进行调整,防止压力过大卡住带钢造成尾塔;
4) 卸卷小车时序修改 F3 抛钢一次上升,F7 抛钢二次上升,尾部进侧导板时上升顶住钢卷,避免了厚硬规格助卷辊压不住造成的松圈现象;
5) 对一些重要检测原件,采用双原件检测方 式,避免单个出现故障影响设备动作。
4.3 操作规范
1)专业间技术交流和学习,提高自动化控制理论和实操理论。提高作业技能,减少人为原因产生的异常卷;
2)制定点检作业标准,对一些重要检测元件的检查、维护重点学习并能学以致用;
3)制定工艺件更换周期,与机修专业做好更换、检查、调整记录,做好初始化工作。
5 结束语
卷取作为热轧线后面一道工序,通过采取相应措施,可减少并控制异常卷率,减少异常卷处理切损,提高产品成材率和经济效益。