中钢1号1280mm高炉中休及停、开炉实践
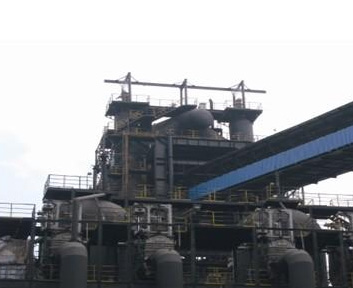
摘要:通过炉顶打水空料线,将料面降到风口带,对破损冷却壁水管进行处理,对破损炉墙进行喷补造衬,以达到合理的炉型。开炉后,炉渣中(Al2O3)在15%以下,(MgO)在8.5%左右,对本次开炉快速达产起到了积极有效的作用。本文重点总结了高炉在喷涂造衬停、开炉过程中的成功经验与操作不足。
关键词:高炉停炉喷补烘炉开炉
1 引言
中钢1#-1280m3高炉设计20个风口及两个铁口,呈180°布置。炉顶采用WP无钟炉顶,炉底、炉缸采用了“碳砖+陶瓷杯”和水冷炉底结构。高炉于2010年9月26日投产,到2015年11月17日停炉中修,共产铁水5837351.14t,单位炉容产铁量4560.43t。在服役近5年零两个月期间,整体炉况稳定顺行,没有出现过大的炉况失常。但是随着炉役进入中后期,高炉本体冷却壁水管破损比较严重,到本次停炉前共计破损83根水管,主要集中在7~9段(42根)和12段(22根)。这不仅制约着高炉经济技术指标的提升与优化,威胁着高炉生产的安全、稳定与长寿。因此,经公司研究决定, 1#高炉停炉中修,对本体水系统进行改造,同时,炉内进行喷补造衬,厚度约为150~170mm。
2 空料线停炉操作
2.1 停炉前的准备
停炉前维持高炉顺行是安全停炉的基础。为此,高炉操作提前三天有意识地采取了活跃炉墙、适当发展边缘的装料制度。配加一定比例的锰矿洗炉,过程中维持充沛的炉缸温度和适宜的炉渣碱度,以达到活跃炉缸的目的。
(1)11月14日14:06将炉料结构由A80%+Q20%调整为A79%+Q21%,炉渣二元碱度下调0.03,同时加锰矿500kg/批,以改善渣铁流动性,确保炉缸活跃。
(2)配加锰矿洗炉时,装料制度由C37235232.5230.32232↓O37335332.5330.32↓变为C37235232.5230.32232↓O37235332.5330.32↓,料线1.3m,以适当发展边沿的气流冲刷炉墙粘结物,为停炉喷补造衬创造良好条件。
(3)11月17日6:00改全焦冶炼,锰矿300kg/批,矿批由33t缩为26t。焦炭负荷由3.86分次退到2.30,确保了炉温充沛,停炉前生铁[Si]为1.30%~1.60%,铁水物理热充沛。
(4)制作了四根炉顶打水管,要求伸入炉内有效长度3700mm,打水管前端堵死。其表面分段打三排直径Φ4mm的打水孔,以保证打水时有良好的雾化效果。
2.2 预休风、空料线操作
11月17日14:30开始有意识地空料线,在顶温上升到220℃左右时压料降温。到休风时料线预空至6.0m左右,加盖面焦48吨。于11月17日16:24~17:27进行预休风,休风共计183min。预休风期间作了以下预备工作:
(1)安装炉顶打水装置。从炉喉十字测温孔处安装4根长4.5m,直径Φ42mm,厚δ4mm的打水管,在水管前端3.7m范围内,分3段交错开孔。水管前端封死,并接通高压水源,四个方向打水管均装有控制阀门和水流量表。
(2)从上升管处改接一根φ32mm煤气取样管,并用φ32mm的黑胶皮管引到风口平台。
(3)处理煤气系统,全开并固定炉顶大放散。关闭重力遮断阀并封沙,关闭布袋进、出气盲板阀。
11月17日19:27复风空料线,煤气全部放散进大气中。空料线开始不久,当风量达到既定风量2300m3/min时,风压127kPa,顶温200℃左右。在20:03发生大爆震一次,顶压由14kPa突然升至65kPa,立即减风100m³/min进行控制。当顶压在不断下降的同时,又伴随着一次小爆震,过后恢复正常顶压12kPa。这次爆震主要是初期打水量控制过大所致。之后,于20:49又大爆震一次,顶压由12kPa上升到28kPa,减风100m3/min控制;21:17第三次大爆震,顶压由13kPa突然升至62kPa,及时减风100m³/min控制,随后连续发生三次小爆震。为了减少或避免爆震,之后将顶温控制280℃~350℃之间。料面位置测算按150000m³风量下降1米为准进行推算,并按照计划时间节点和对料面测算下降位置来控制风量。于22:45减风100m³/min,23:48再减风100m³/min,后期降料面过程中未发生爆震现象。到18日5:30风口陆续出现挂渣、吹空现象,并打开铁口出一次铁。到6:30全部风口吹空见黑,停炉顶打水,结束空料线操作。
此次,1#高炉采用炉喉雾化水装置与十字测温打水装置结合的方法进行空料线。在空料线过程中虽发生大、小爆震8次,但没有发生煤气爆炸和其它设备、人身事故。空料线比较顺利,基本上达到了既迅速又安全的预期目标。空料线共耗时11小时,比计划测算时间提前了2小时,累计耗风量为158wm3。
3 喷补造衬操作
3.1 喷补前准备工作
在11月18日6:30空料线结束后,又继续送冷风凉热风总管,至19日8:30具备喷补进炉作业条件。炉前卸下全部风口小套、直吹管,风口中套以两铁口为中线,共卸下10个。并将炉芯残余死焦柱扒平,加河沙8m3压火,目的是用来隔绝空气,阻止炉内焦炭继续燃烧,防止炉缸温度进一步降低,也便于清除喷补反弹料。由于本次停炉空料线前洗炉比较彻底,炉墙非常干净,几乎无粘结物。所以,喷补前仅对炉墙进行了简单的清洗。于19:00开始安装喷补造衬设备,同时对破损冷却壁进行确认处理,以便于安装铜冷棒;对局部无冷却壁区进行补焊锚勾,以便于喷补料能与炉墙牢固结合。
3.2 高炉喷补造衬作业
11月21日16:10开始喷补,这次喷补是自上而下分为三个阶段进行的。第一阶段按照50~80mm的厚度进行喷补找轮廓;第二阶段按照50mm左右的厚度喷补;第三阶段按照30mm左右进行喷补。由于喷补过程中粉尘比较大,加之料固结比较快,我们为有效保证喷补厚度,要求每隔两段冷板在其缝隙处插入150mm的标尺,并以此作为核实喷补厚度的衡量标准。同时,过程中及时清理反弹料进行二次利用。整个喷补到11月23日7:00结束,共计39小时,用料223.14吨,反料率为3.59%,控制在技术要求的5.0%之内。
4 高炉烘炉、开炉
4.1 烘炉
高炉于11月29日16:30开始烘炉,至12月2日8:16烘炉结束,共用时约65小时,比计划延长了21小时。而且在烘炉过程中进行打压检漏和停风处理热风总管漏点,导致烘炉未能持续进行,导致烘炉曲线波动比较大。在烘炉过程中由于兼顾热风总管、竖管烘烤的限制,且在铁口孔道未安装临时烘炉热电偶,只能通过热风温度间接地反映炉缸温度的变化。因而烘炉风量没有按要求达到1200m³/min,影响了高炉烘炉效果。实际烘炉曲线如下图1。
4.2 开炉冶炼参数的确定
为确保本次开炉的顺利进行,高炉相关技术人员经过多次商讨后确定全炉焦比:3.45,正常料焦比:0.80;正常料碱度:0.95;空焦碱度:0.85;炉渣(Al2O3)≤15%,(MgO)=8.5~9%;料线取1.5m;正常料压缩率11.5%,空焦压缩率13%,净焦压缩率14%;矿批15t;焦批7.28t。入炉矿配比:烧结85%+球15%;铁水控制要求:[Si] 3.50%,[Mn] 1.50%,[Fe]91.5%,[S],0.060%,铁水温度>1470℃。
4.3 开炉装料
本次开炉装料从下至上分别为铺底焦、净焦、空焦、正常料+空焦、正常料。原计划带风装料,实际考虑到炉缸焦炭炽热会着火,改为静态装炉。
2015年12月2日10:10开始装料,装铺底焦7批,装净焦26批,装空焦20批,装轻料(正常料+空焦)26批, 12月2日21:10装料完成累计装料耗时11小时。在装料过程中为了尽可能做到料面平整,每五批调整布料角度一次。由于前期配料计算选取参数准确,以及喷补后炉容再测算比较到位,各段料组实际装入高度与理论测算几乎无差别。具体见装料记录表1。
4.4 高炉送风点火
12月2日22:30送风点火,开炉堵4#、5#、6#、7#、14#、15#、16#、17#风口,用12个风口送风。初期风量800m³/min,热风压力50kPa,透气性指数15.9,顶压9kPa,风温750℃,顶温24℃。同时,两铁口安装专用氧枪向炉内吹氧、吹风,目的是尽快加热炉缸(炉缸内积存的渣、铁热量严重不足,几乎完全是凝固状态)。
12月3日1:00许,风量1000m³/min,热风压力98kPa,透气性指数12.4,顶压14kPa,风温800℃,顶温42℃,此时炉内出现憋压现象。到3:00风压上升至198kPa,风量萎缩至660m³/min左右,于3:15休风坐料处理。3:23复风,风压22kPa,风量520m³/min左右,风温760℃,顶温24℃。之后,炉况恢复比较顺利,到8:00风量恢复至1064m³/min,风压51kPa,风温820℃,顶压8.7kPa,顶温36℃。12:20风量恢复至1460m³/min,风压90kPa,风温850℃,顶压18kPa,顶温42℃。
12月3日7:45,南场铁口预埋氧枪自动烧开,出铁约3.5t后堵口;到10:13北场铁口氧枪也烧开,出铁约5t后堵口。13:15累计耗风量达到107wm3预计第一批铁料已进入炉缸,组织南场出第一炉铁。由于炉外准备充分,安全出铁约20t。炉温[Si]2.86%,[S]0.060%,[Mn]1.50%,铁水物理热1274℃。由于首炉铁口开口顺利,渣铁流动性相对较好,送风15.5h后,于13:42开14#风口。到14:20风量加之1529 m³/min,风压92kPa,风温920℃,顶压18.6kPa,顶温67℃,南尺3.84m,北尺3.83m。同时,矿批由15t扩到16t,料制:C322302282222↓O305285↓变为C342322302222↓O325295↓,并且下料以料线4.0m为准。14:44开北场铁口,出铁约10t,炉温[Si]5.28%,[S]0.022%,[Mn]2.34%,铁水物理热未测。之后随着开风口数目的增加,风量逐步增加,料线也逐步回至2.0m。
在此期间,11:30炉顶煤气化验合格。但是由于顶温迟迟起不来,一直到15:00顶温达到70℃时开始引煤气关放散,并于15:50开4#风口,23:25开5#风口;21:20开7#风口;21:30开17#风口。直到12月3日24:00时, 已有17个风口送风,风量达到1800m3/min,风压120kPa,风温830℃,顶压55kPa,顶温260℃。
12月4日00:00开始依次将北场铁口,南场铁口角度由10°调到12°。但是,调整铁口角度之后,先是北场铁口出现难开现象,一直烧不开持续到9:00,采用炸药开口;接着是南场铁口也出现难开现象,于11:30炸开。考虑到可能是由于炉缸热量不足,半熔融渣铁未能彻底化开,再次将南、北场铁口角度由12°调到6°,以确保渣铁顺利排放。同时,炉内恢复进程也加快,分别于5:15、13:56、17:10开15#、16#、6#风口,也就是说在送风点火43小时内,达到20个风口送风状态。
12月5日,随着炉缸温度的回升,渣铁流动性改善,逐步将两铁口角度由6°恢复到10°,同时,炉内恢复节奏也随之加快。到12月5日2:00开始喷煤,8:50开始富氧30m3/min,焦炭负荷达到3.36。到11:40风量恢复到2410m³/min,风压230kPa,顶压144kPa,顶温210℃左右,风温1010℃左右,矿批25t,负荷3.55,炉温控制在[Si]2.0~2.5%,料制恢复到C362342322302222↓O363343322302↓。于12月6日7:30料制恢复到C372352332312222↓O373353332312↓,料线恢复至1.5m,炉温按照0.8~1.2%控制,于13:30投用TRT。
5 结 语
(1)停炉前三天退负荷,采用适当发展边缘气流的装料制度,并且配加锰矿洗炉,为安全顺利空料线停炉提供了有力保证。但空料线前、中期,因风量使用较大,打水量控制过大,使炉顶温度波动大,发生两次大的爆震,值得吸取教训。今后在空料线初期时,一定要结合炉顶温度控制打水量,确保顶温大于250℃。
(2)通过这次空料线实践表明,焦炭负荷退40.4%有所过头,也就是说焦炭负荷退至2.30时,炉温略有偏高,应退至2.50即可。
(3)在喷补过程中,一定要控制好进料量和配加水的比例,避免过程中料干扬尘大,反弹料较多。尽管是二次回收利用,返料率达到控制目标值5%之内,但是过程中往往出现堵枪现象,影响了喷补速度。
(4)对于中修高炉开炉,初期加风、开风口不可过急,否则,容易引起高炉难行悬料。同时,由于炉缸透液性差,铁口角度应调整到尽可能小,以利于快速排放炉缸积存“冷”渣铁,应避免角度过大,铁口过深,凝铁层难开的现象发生。
(5) 由于准备工作充分,本次空料线过程只耗时11小时就成功实现,并且于12月2日22:30送风点火后炉况顺行。43个小时恢复全风口作业,51h30min恢复喷煤,12月10日产量达2569.89t(扣除渣量),利用系数达2.178t/m3·d,达到了设计产能,实现了安全快速降料面、顺利开炉、快速达产的目标。