Process improvement of pinch roll in high speed bar production line
Abstract: High speed bar products are generally used in the cooling bed after the segment of the first pinch and then brake. The finished products will produce pinch marks on the surface after the pinch roll, which will affect the surface quality. Through analysis, the groove configuration of the pinch roller is optimized, and the pinch marks are basically eliminated and the surface quality of the bar is improved under the condition of guaranteeing the height of the transverse rib and the longitudinal rib.
At present, high-speed bar production lines generally use 45° top crossover finishing mill to produce finished products, and the finished product speed is 30 ~ 40 m/s. The high speed flying shear ensures the dimensional accuracy of bar segmentation and shearing, the brake roller and the rotating hub feeding mechanism ensure the braking of the bar and the stability of the straightening plate falling into the cold bed. This production method provides another reliable and efficient way for the production of small and medium-sized bar products. However, when the finished product is cooled by the clamping brake, there will be pinch marks on the surface of the clamping brake, which will affect the surface quality of the product.
1, high bar production line pinch roll process layout
Shougang Changzhi Iron & Steel Co., LTD. (hereinafter referred to as Changzhi Iron & Steel) bar line composite production line after the high bar area rolling, a total of three sets of pinch roller. The first pinch roll of flying shear is set to achieve double size cutting accuracy; No. 2 and No. 3 pinch rollers are set up to realize the pinch and brake of the double ruler after rolling, so that the double ruler smoothly enters the hub and stably falls into the cooling bed straightening plate. The process layout is shown in Figure 1.
2, the product surface pinch marks cause
1) The indentation is serious after the hot rolled ribbed steel bar is cooled on the brake in the high-speed bar production line, which affects the surface quality of the finished product.
2) When the production capacity of the pinch roller exceeds 2000t, the contact part of the ribbed steel bar and the pass of the pinch brake roller is seriously worn, and the pass part of the pinch brake roller is worn with grooves, which will indentation the surface of the transverse rib and the longitudinal rib again during the pinch brake process, causing secondary damage [2]. The wear parts of the pinch brake roll are shown in Figure 2.
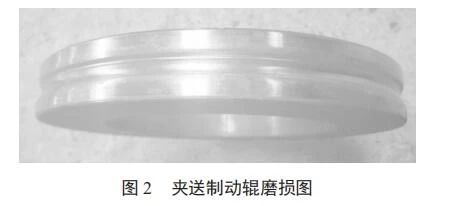
3) The pass shape of the pinch brake roll used for high-speed bar is elliptical pass shape, which has poor clamping effect on the bar at the moment of clamping, and the twisting and shaking situation in the pass shape is one of the reasons for wave bending in the rolling of small-size high-speed bar.
3, high speed bar clamping process stress state analysis
High speed bar finishing mill usually adopts 45° top crossing arrangement, the longitudinal rib and horizontal Angle after finishing the ribbed steel bar are 45°, and the pass shape of the pinch brake roll is horizontal arrangement. When the stable pinch is in the state, the transverse rib and longitudinal rib contact directly with the pinch brake roll (see Figure 3), basically along the direction line of the rolled piece, the contact area is small, and the wear is fast.
4, pinch brake roll pass and configuration improved
The clamping Angle of the pinch roller is changed to 45°, which is consistent with the direction of the finished roller ring of the finishing mill, so as to ensure that the clamping area is increased as much as possible while no torsional force is generated when the finished product is running at high speed after rolling. This method can not only ensure the stable clamping effect but also ensure the surface quality of the product [1]. This method needs to change the pass shape of the pinch roller, reduce the tangential expansion Angle, and improve the clamping stability [2]. After the improvement, the pass diagram of the pinch brake roll is shown in Figure 4, and the pass configuration diagram of the pinch brake roll is shown in Figure 5.
5. Operation effect
By improving the pass shape of the pinch brake roll and the Angle of the matching roll, the pinch roller only contacts the transverse rib during the pinch process, the contact area is increased, the stability of the bar clamping is improved, and the pinch marks are basically eliminated. At the same time, the torsion and jitter of the finished product in the process of clamping brake are further improved, and the service life of the clamping brake roll is increased.