高速线材在线全自动切尾功能探索及应用
摘要:高速线材在斯太尔摩冷却线到集卷收集筒之前,线材尾部一直为人工剪切,通过使用机械人手臂对线材尾部自动剪切进行可行性分析论证,并且阐述设备在现场安装、调试以及初期的使用,实现了自动尾部剪切的一种实践探索,为国内众多的高速线材生产线提供一种有益借鉴。
目前全国有高速线材生产线600余条,高速线材生产线的特点是线速度高,一般在80-120m/s左右;连续性生产,节奏快,生产效率高。由于工艺特性和用户要求,线材的头尾部分在打捆前必须切除一部分(头尾的尺寸、耳形或因不穿水强度不符等因素不能满足下游客户使用要求的部分)。线材的头尾剪切各生产厂因装备不同而异,常见的是小规格(8mm以下)线材尾部在STELMOR辊道线上人工剪切,头部以及大规格(8mm及以上)头尾是在P&F线上进行人工机械辅助剪切。由于工艺装备决定的因素,在集卷后P&F线切尾工位C形钩上进行线材尾部剪切,因线材尾部处在C形钩的闭合侧,无法剪切一个点而将多圈移出,必须多圈的每圈剪切才能实现剪切后的尾圈移除。众所周知,线材P&F线系统除了为生产线提供集卷运输、头部剪切、尾部剪切、打捆、称重、卸卷等工位的功能外,另一个重要的功能就是实现线材的降温冷却。大规格线材生产有节奏快、线卷温度高、产量大的特点。因此大规格生产线的P&F线头尾剪切工位一直存在工作量大、体力劳动强度大、环境温度高的“两大一高”问题。
在线全自动切尾功能的智能化建设的目的,就是要实现以人为本,切实改善员工工作环境,减轻员工劳动强度,保持产线安全高效生产。本文介绍的是大规格线材产线的线材尾部在STELMOR辊道线上进行智能控制的机器人全自动剪切。
2、可行性分析
工业自动化和智能化技术的发展,为轧钢生产线运用机器人替代人工作业提供了条件,环境复杂岗位、重体力劳动岗位被机器人替代的设想也越来越多,论证线材STELMOR在线全自动机器人切尾替代P&F线上人工机械辅助切尾的可行性具有重要意义。
2.1作业空间与环境
大规格高速线材生产线的设计,一般均充分考虑高端线材产品生产对装备的要求,STELMOR辊道的设计有调节余地大,预留空间大的特点,在线增设机器人切尾设备,在作业空间上没有限制。
机器人位置增设在STELMOR辊道最后一段,各种规格和钢种,在机器人作业时的最高环境温度不超过250℃,为机器人允许的作业温度。
2.2生产作业节奏衔接
高速线材生产线有连续性、节奏快的特点,正常生产时的出钢间隔一般在3.5秒左右。因此要求机器人从尾部拨料到剪切完成的最长时间不能超过3.5秒。而机器人系统响应时间是ms级,两台机器人协调时有同步启动空间,两台机器人作业的并集时间控制在出钢间隔周期内的空间是可行的。
2.3剪后尾料处理方式
对于中大规格生产线,成品尾部吐丝圈形比较规则,无论是剪后STELMOR辊道上在线收集,还是剪后跟随母件或与下一件头部一起入筒收集都有其可行的途径,用户可以按生产线实际作业环境或作业习惯自行选择。
2.4剪切不成功信息的传递
线材尾部在STELMOR辊道上剪切以后,一般后道P&F线上就不再设置切尾岗位。但机器人在线剪切成功率很难做到100%,一旦有尾部剪切不成功的线卷,就必须让后道切头岗位进行补切,以防尾部漏剪流入用户。因此机器人在线剪切不成功信息如何及时传递给切头岗位人员是必须思考解决的问题之一。若产线选择剪切尾料与下一件头部一起入筒收集的方式,即在线剪切的尾料挂在下一卷C形钩上的头部,由P&F线切头岗位的操作工将上一件料的头部从C形钩上取出收集。如果操作工没有取到尾料,说明上一件成品没有成功切尾,因此就必须在预留好的尾部剪切工位进行尾部补切。这说明剪切不成功信息传递是能够实现的。
3、设备安装及调试
3.1装备选择与安装
线材生产线斯太尔摩辊道上方安装可旋转支架,支架上方安装2只探测器,同时在辊道旁安装两只机械手装置,一只机械手附带挡料装置,另外一只机械手附带钩料及剪切装置,钩料由气缸驱动,剪切由液压驱动(见图1)。
高速线材正常生产时,斯太尔摩辊道速度不大于1.5m/s,过钢间隔不小于3.5秒,线材经过吐丝机成圈形后通过斯太尔摩辊道运送,当线材尾部通过探测器位置时,探测器送出信号给两台机械手,挡料机械手、钩料剪切机械手接受到信号后延迟动作,运行至工作位,挡料装置下降使线圈尾部保持静止,线圈在辊道里拉开距离,然后钩料剪切机械手上的钩料装置下降,挡料装置上升,线圈前进进入钩料装置,钩料装置把线材提升至剪切装置的刀刃口,然后对线材进行剪切,完成剪切动作后再把剪切下来的尾料放入辊道中。
装置为国内试制的首套线材在线自动切尾设备,于2019年4月安装,经多次改进,7月份开始热负荷调试。
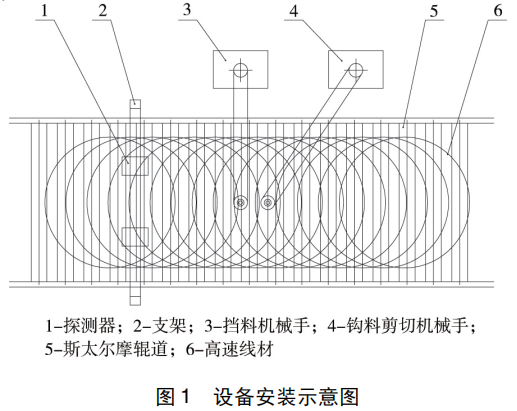
因是国内首套智能全自动剪切装置,从保护设备的角度出发,制定了热机调试方案,调试期出钢间隔从15秒开始,逐步缩短到目前的5秒,但离轧制间隔3.5秒目标,还有1.5秒的差距,目前正与设备供货方共同制定调试方案,进一步优化。
4、问题与处理方法
国内首套智能全自动剪切装置的调试,暴露了部分问题,通过问题分析和攻关,一些问题得到处理,部分问题仍在改进中。
4.1双机不动作
调试中出现挡料机械手和钩料剪切机械手同时不动作现象,主要是线卷尾部检测激光探测器无反应或反应超时(设定2s)所致。通过检查和延时调整已得到处理解决。
4.2剪料不成功
剪切不成功包括未钩到料、钩双料、未剪断等情况,主要与挡料机械手延时设定、剪切机械手刀片失效有关,通过延时调节和刀片更换得到解决。
4.3倒叉料
该现象是指钩料剪切机械手剪切后,母材尾部几圈线卷出现圈形倒叉的现象,由于圈形倒叉,极易在线卷进入集卷筒时产生卡钢事故。产生倒叉料的主要原因是钩料剪切机械手钩料提升剪切时,其钩料抬升高度过高,且钩料后剪切动作的延时时间过长,使母材尾部几圈线卷被拉开,弹力变大,在抬升剪断后尾部弹回时非原位恢复,而是错位回弹,造成倒叉现象。处理方法是合理调整抬升高度,适当缩短钩料后剪切动作的延时时间。
4.4剪切圈数不稳定
线材生产线的线卷尾部剪切圈数在工艺中是有明确标准的,但调试中发现成品剪切圈数并不稳定。如果剪切圈数不稳定,剪切圈数少了可能带来成品质量问题,剪切圈数多了则会造成成材率指标的下降。该装置剪切圈数的设定是依靠激光探测器信号、STELMOR末端辊道速度和挡料机械手动作延时时间来综合计算的。由于受检测灵敏度、响应灵敏度和尾部吐丝状态的影响,综合计算的圈数与实际剪切圈数的对应性较差。下一步对挡料机械手动作时间的设定,除自动采集R末端辊道速度外,还需机器人系统与生产PLC系统打通,自动追塑采集被剪切卷吐丝时的尾部吐丝线速度,以精准计算尾部剪圈数。
4.5物料跟踪系统融合
全自动剪切系统有完整的故障记录系统,而线材生产线也有完整的在线物料跟踪系统。剪切不成功信息传递暂时性依靠切头操作工在C形钩上是否取到尾料来判断。但全自动剪切系统与产线在线物料跟踪系统融合后,可根据全自动剪切系统发出的剪切不成功故障信息,自动跟踪到线卷的挂钩钩号,利用C形钩上FRD卡,由P&F线成品切头岗位前的读卡器识别,做到自动报警提醒,提高成品切头尾工序质量运行的稳定性。
5、结束语
项目从施工到调试大概4个月时间,虽然离正常轧机节奏3.5秒,还有1.5秒的差距,但相对于调试初期的15秒已经有很大的进步。自动剪切的成功率从调试初期30%到现在的90%左右,与投入工业化正常生产的要求还有一步之遥。
随着物质、生活水平的不断提高,钢铁行业工作量大、体力劳动强度大、环境温度高岗位的机械化、自动化、智能化改造变得迫在眉捷。而当今信息技术、制造技术的日新月异,也为这些岗位的改造创造了条件。该高速线材生产线在线全自动切尾功能的建设应用。
2024/02/06 11:01:26
619 次